When La Marzocco added the Swan this year, the factory production lines were ready. Set on the factory’s second floor, La Marzocco’s new production lines were designed to take advantage of something new for this nearly 100-year-old company: smaller machines. With the Linea Mini, Linea Micra, Pico, and now Swan, the factory was able to condense the space needed for production by installing rollers. Now, each of these machines is made by hand on a state-of-the-art production line.
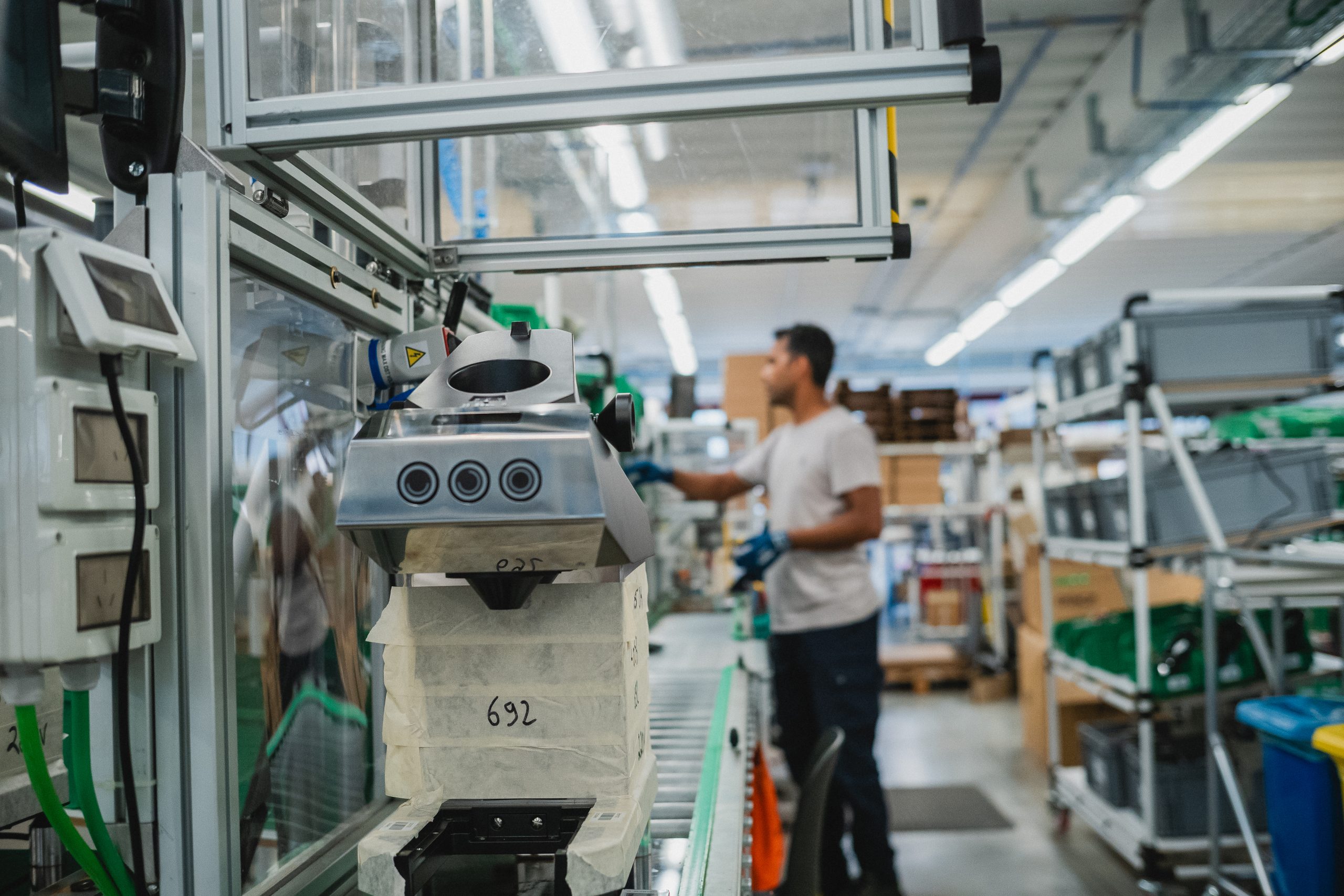
These lines allow artisans to add extreme focus to each task of assembling their machines. Stations are organized with the production engineers to streamline assembly, which ensures that each station allows the artisan to inspect their work as they add new components by hand.
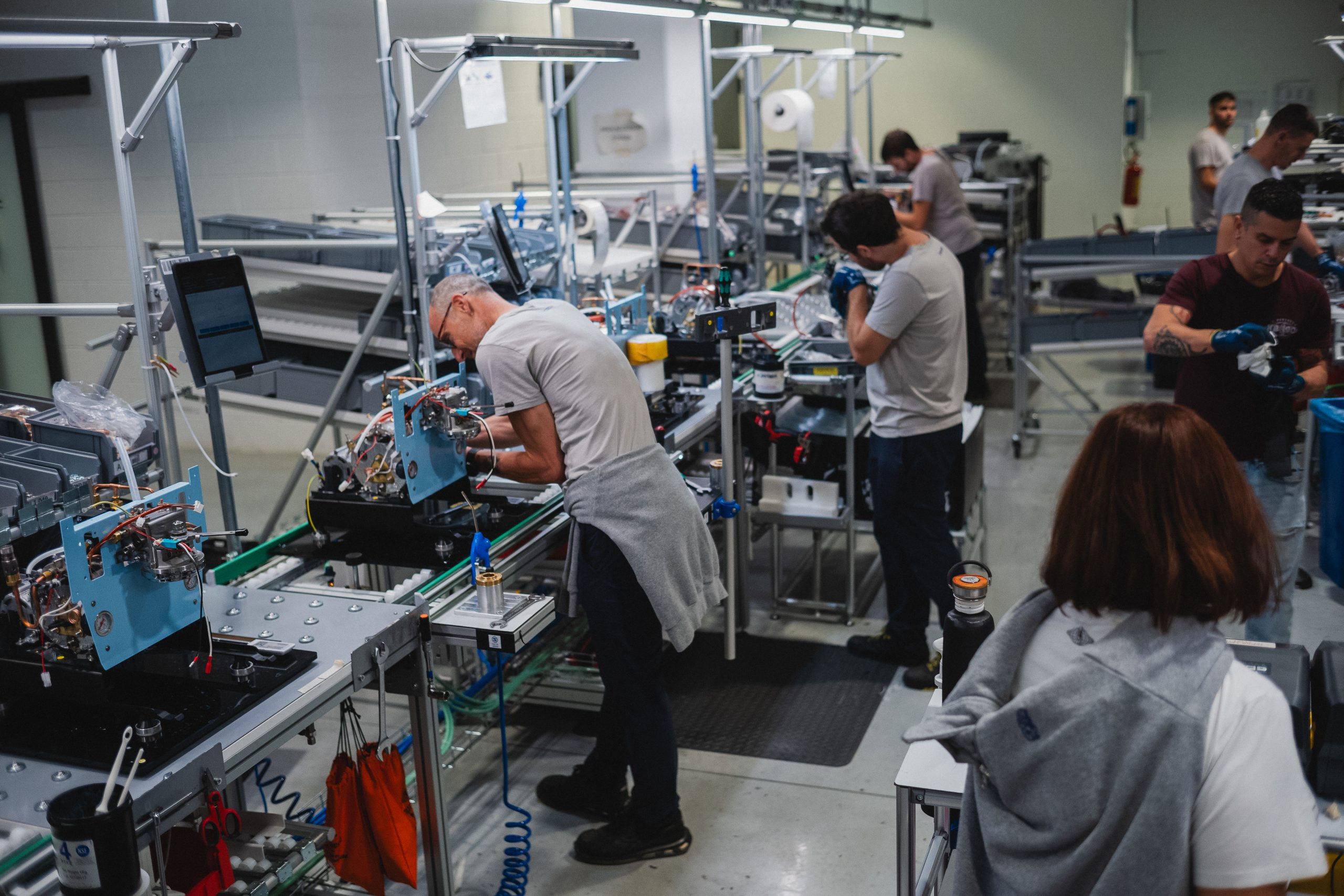
Factory artisans are cross-trained at each station, making sure they’re able to make an entire machine from the ground up.
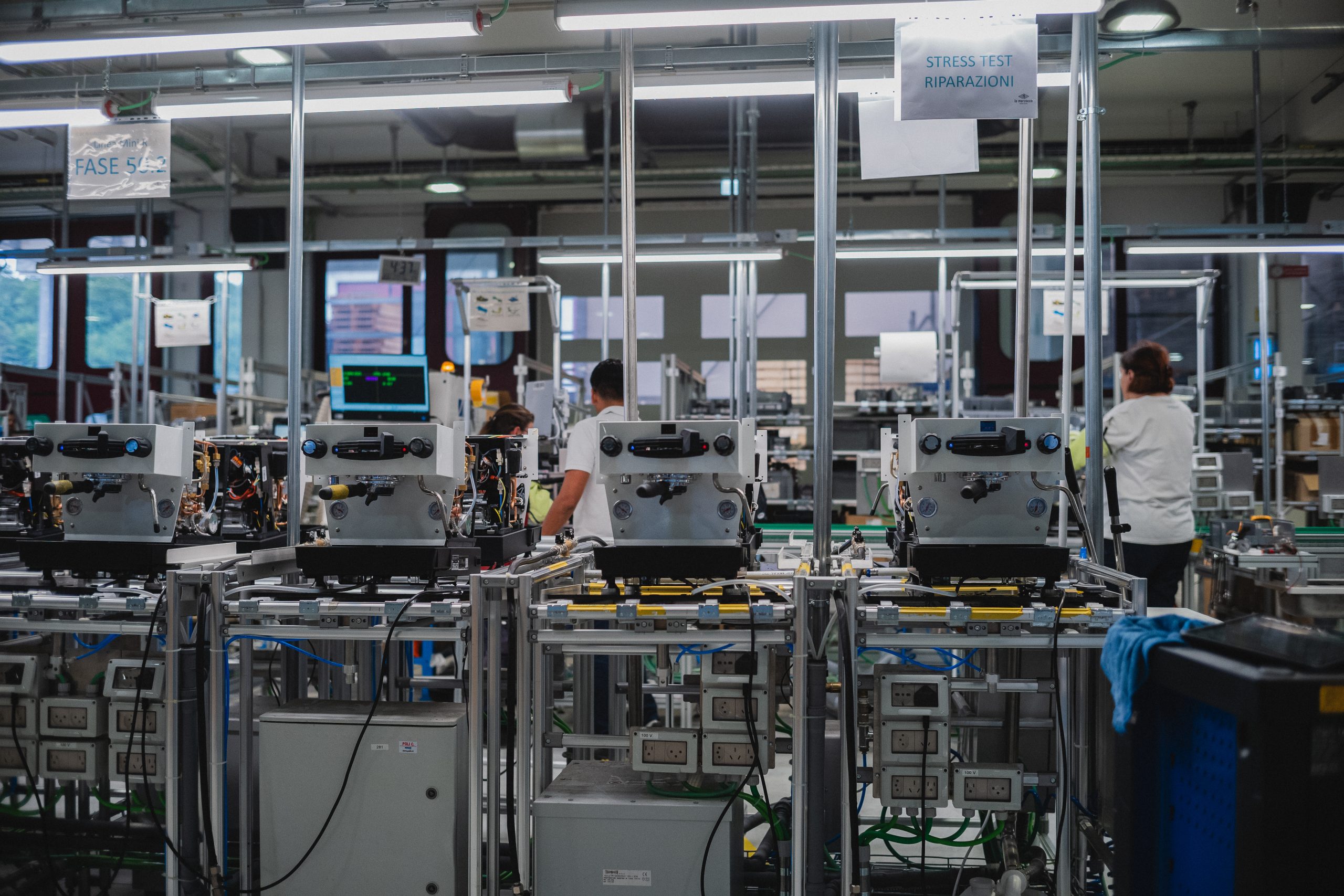
Machines are thoroughly tested during the manufacturing process to meet quality standards. Any machine that doesn’t pass immediate inspection is set aside for further assessment so it can be corrected.
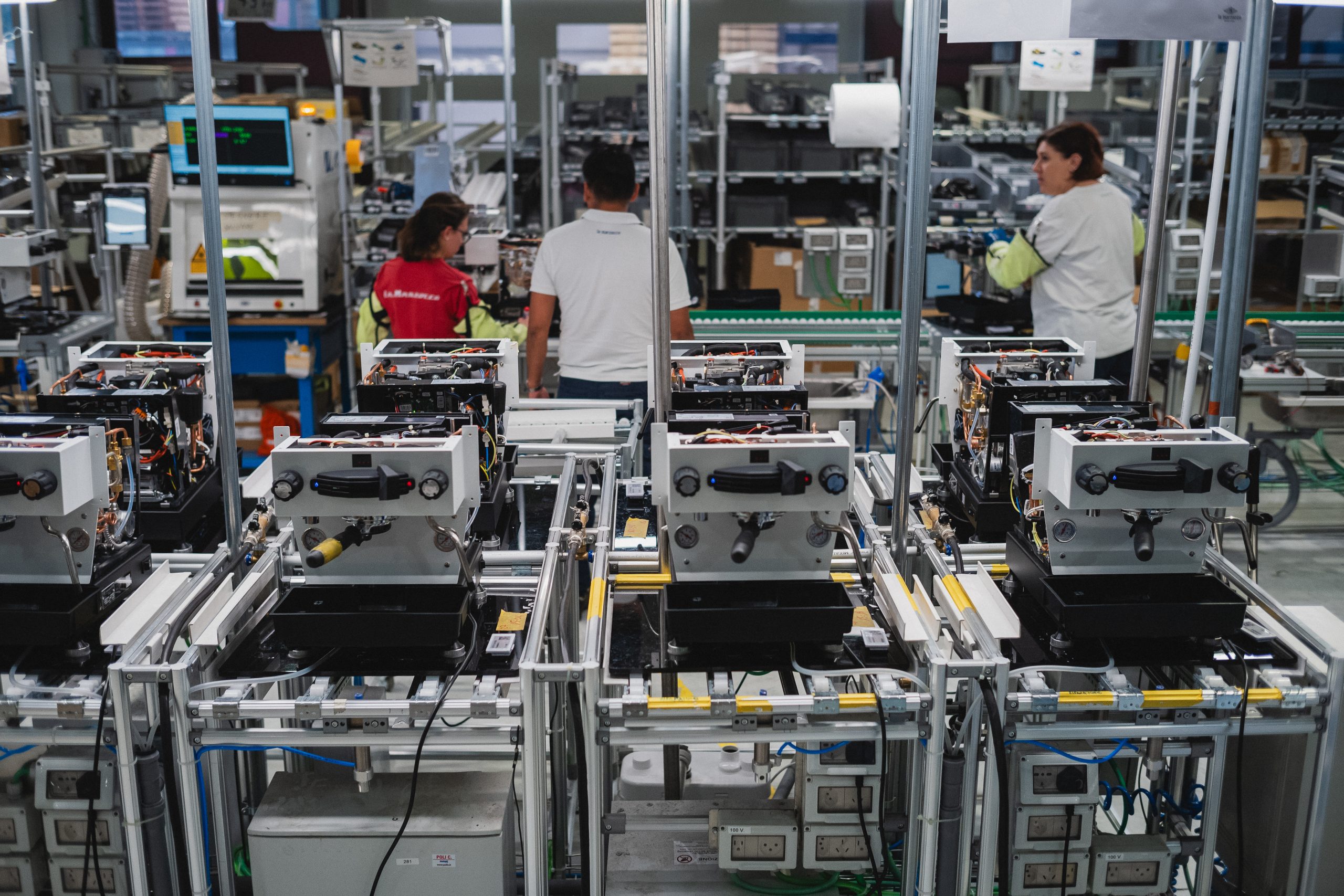
Machines are also tested over time to guarantee their operational status over multiple hours.
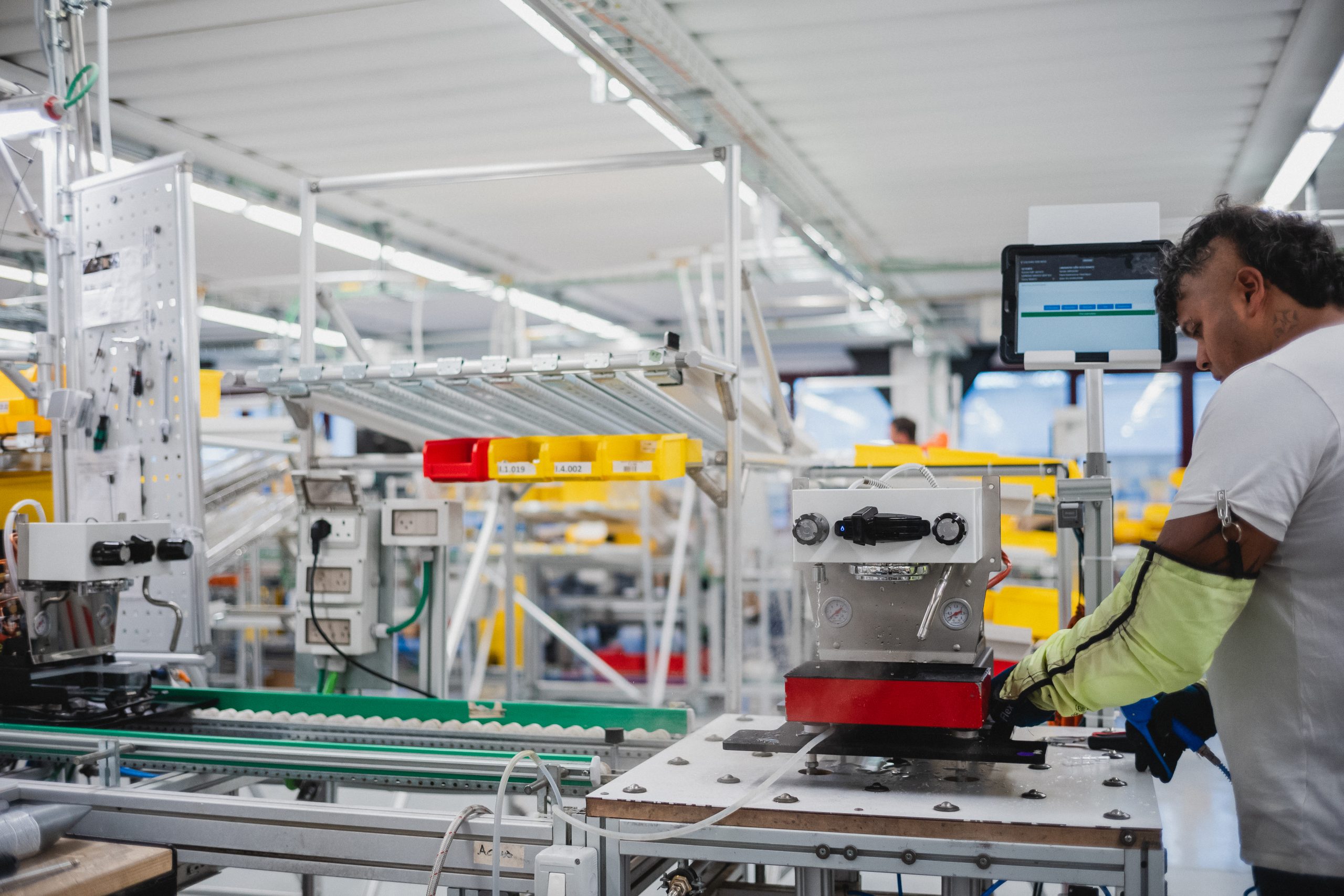
Heating elements, valves, and electrical systems are all checked individually during assembly.
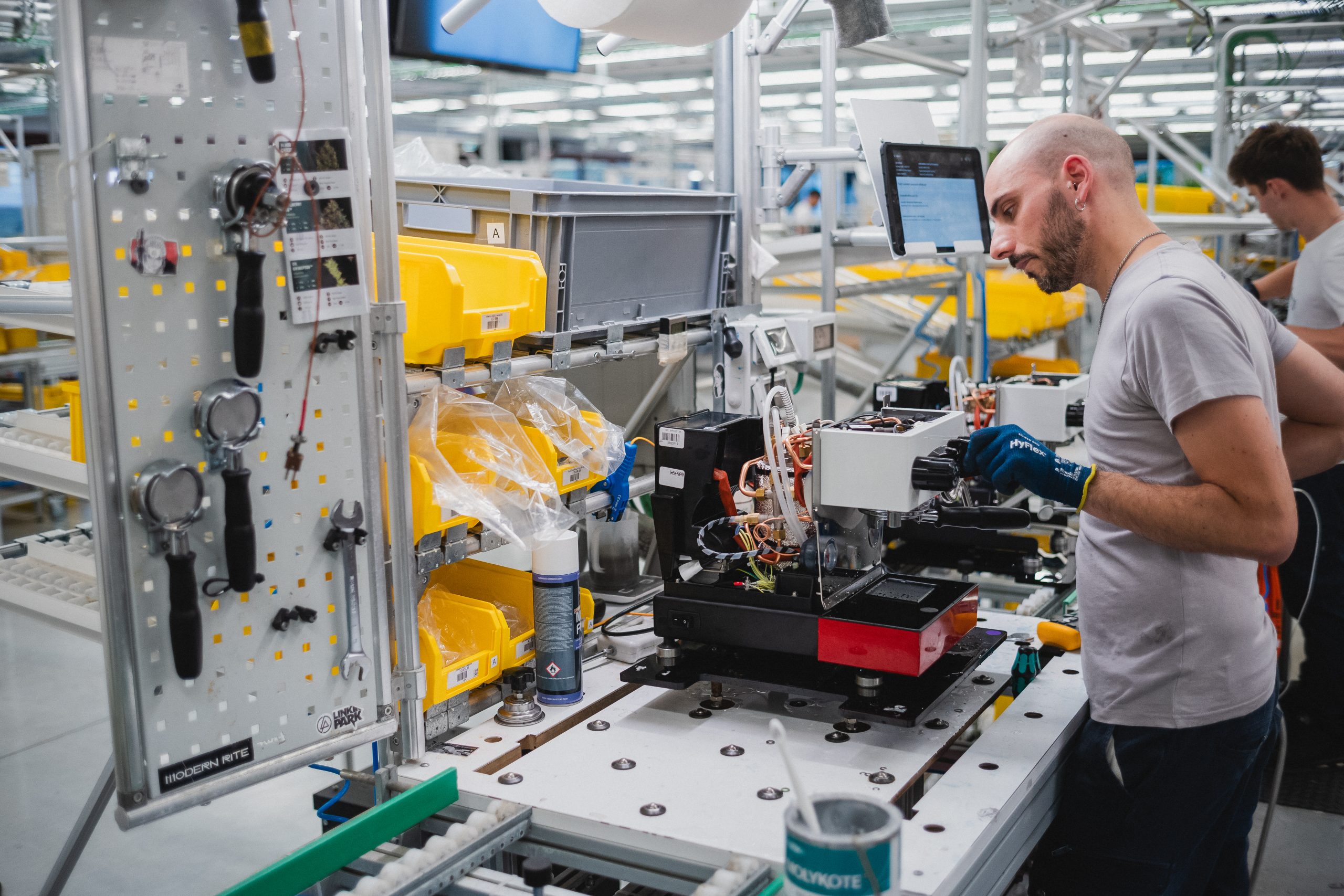
Specialized tools help artisans focus on their specific tasks, like smart screwdrivers that can track the correct number of screws that have been installed at each station.
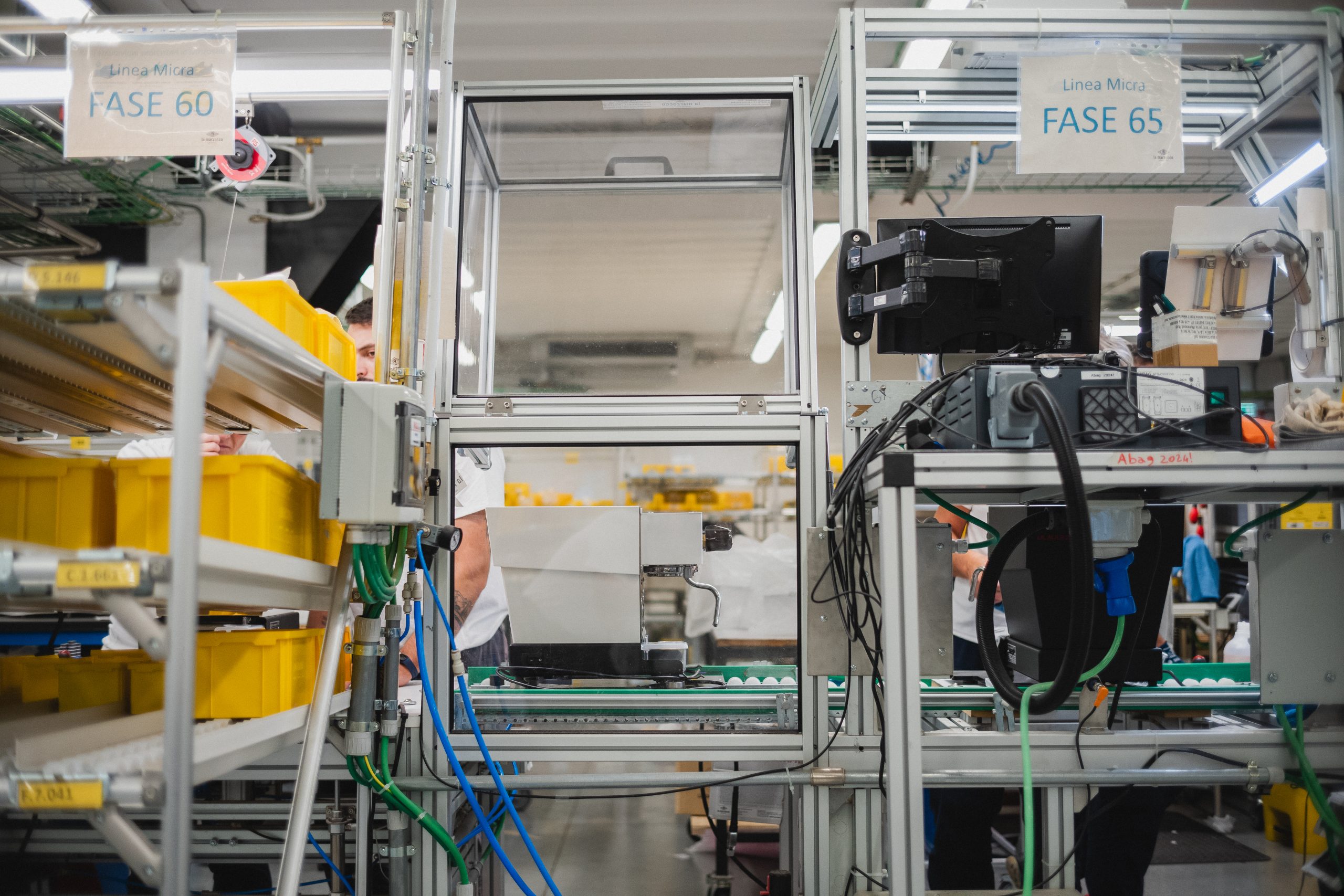
The end of each line is designed for finishing touches, like installing the final panels and polishing each surface. But even at the end of production, even more testing occurs. Even after these Swans have finished production, they’re cycled through extended motor testing to ensure the highest quality standard.
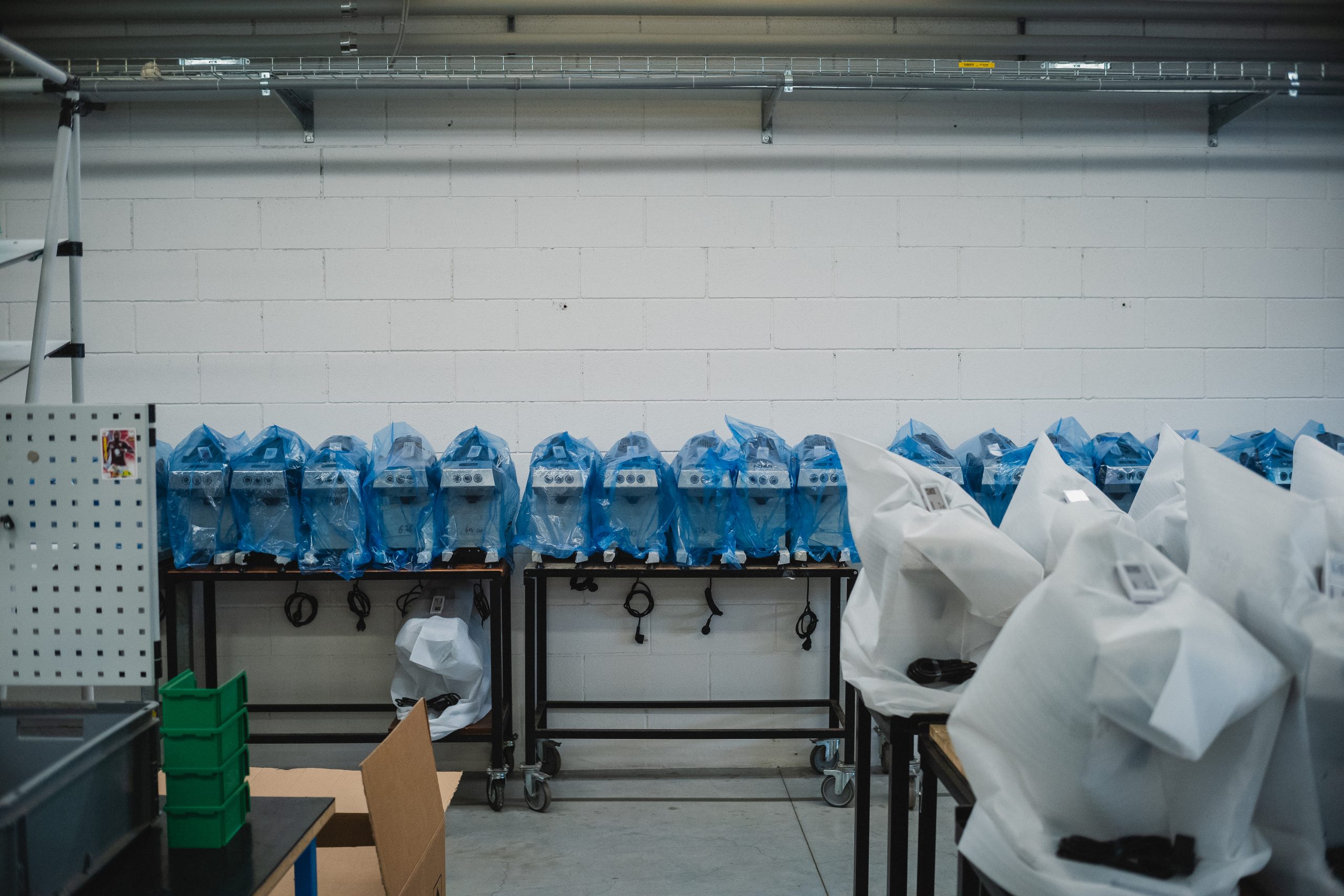